

9
Magnetic clamping technology
Magnetic clamping technology enables lightning-fast workpiece clamping without deformation.
Magnetic chucks are used in all areas of metalworking. Both thin, delicate and very large, heavy workpieces can be held securely in place with the various versions of magnetic chucks. The use of magnetic chucks is particularly beneficial when machining small batches, as the components/workpieces to be machined can be changed quickly.
SPREITZER offers permanent magnetic chucks, electro-magnetic chucks, electro-permanent magnetic chucks, round magnets, electromagnets –the right chuck for every requirement.
Magnetic clamping technology in metal processing
Magnetic clamping technology is used in grinding, milling, eroding and metrology . Magnetic clamping devices prove their worth every day thanks to their high precision and durability. The ability to clamp workpieces quickly and, above all, without distortion is one of the most important strengths of magnetic chucks.
Our magnetic chucks are suitable for use as milling magnets, grinding magnets or eroding magnets.
Advantages of magnetic clamping technology:
- Clamping with short setup times
- Flexible and universal
- Large holding forces
- High clamping forces
- Adapted to the workpiece contour
- Precise quality
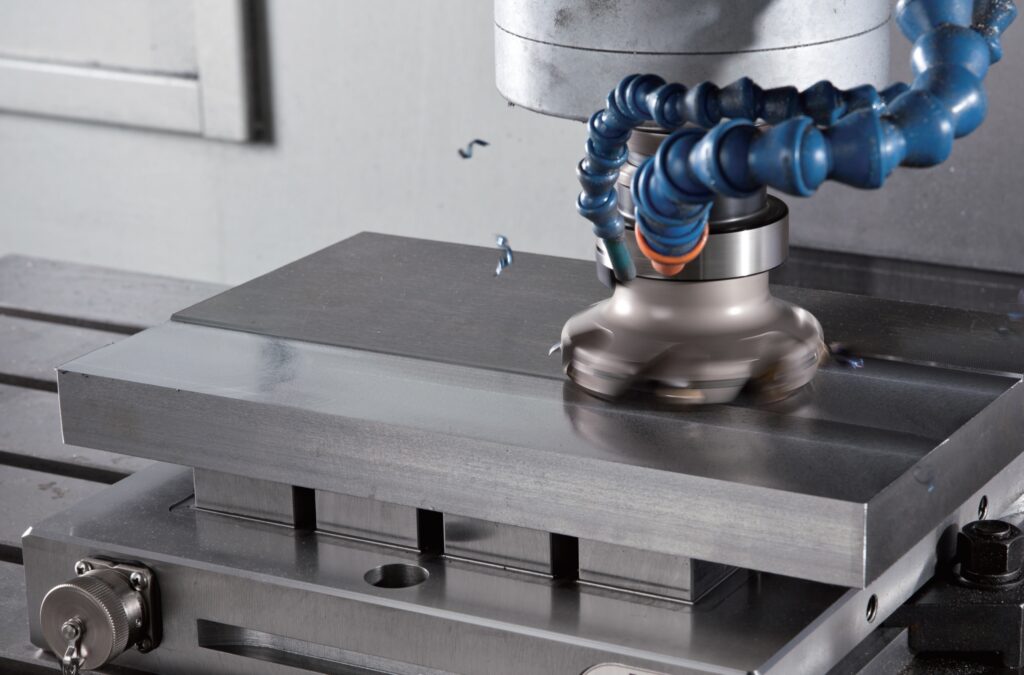
Permanent magnetic chucks
Permanent magnetic clamping technology – The functional principle
Magnetization is achieved by mechanically shifting the internal poles (north/south) by turning the operating key. The magnets opposite the north and south poles are arranged in such a way that the magnetic flux lines are diverted across the surface. The result is the stepless generation of holding force.

The holding force of the magnetic chucks is very uniform, without magnetic dispersion.
SPREITZER offers rectangular and round permanent magnetic chucks
Our range includes permanent magnets with fine pole pitch for grinding and eroding work as well as permanent magnets with coarse pole pitch for milling.
Round magnetic chucks, magnetic clamps with reinforced ceramic magnet system and max pole pitch are used for clamping bulky and heavy workpieces.
The magnetic force is infinitely variable, and centering grooves machined into the surface make it easier to align the workpiece.
Furthermore, a centering hole can be made in the surface if desired.
Strengths of permanent magnetic chucks:
- Manually operated
- Low magnetic field
- No heat delay
- Palletizable
Electro-permanent magnetic chucks
Different designs and sizes of electro-permanent magnetic chucks available on request.
The magnetic clamping plates require only a short current pulse for switching and can be used autonomously.
Without further energy consumption, without disturbing connections.
- Force generation by current pulse
- Force compound through one-time energy supply
- No heat delay
- Low residual magnetism
- Extreme holding forces
- Palletizable
Electro-permanent magnetic chucks with polar extensions
The functional principle
Mounting is carried out without tools using a threaded connection in the magnetic clamping plate. The nominal holding force is transferred to the workpiece through the pole extension. The fixed pole extension acts as a rigid support surface, while the movable pole extension compensates for potential workpiece irregularities of up to 6 mm.


Electro-permanent magnetic chucks with square pole technology, such as the SPQX electro-permanent magnetic chuck , can be extended with mobile and fixed pole extensions. They adapt to the workpiece and hold it securely. The individual contact points between the magnetic clamping plate and the workpiece can be defined individually. Pole extensions allow holes to be drilled through the workpiece without damaging the magnetic chuck. Thanks to the increased contact surface and maximum accessibility, even complex 5-axis machining operations can be carried out.
Electro-permanent magnetic clamping plates with pole extensions:
- Evenly distributed magnetic force
- Deformation-free clamping
- Relining of uneven workpieces
Pole extensions
Fixed pole extensions
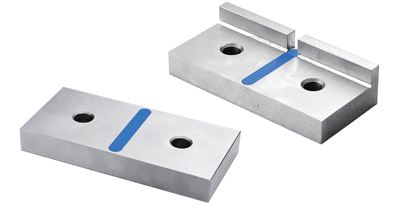
Movable pole extensions

Mobile and fixed pole extensions on the square pole clamping system allow clamping of wavy and warped metal parts.
They adapt to your workpiece and hold it securely.
The individual contact points between the magnetic chuck and the workpiece can be defined individually.
It is also possible to drill through and machine inner edges on magnetically clamped workpieces.
Additional pole extensions can be attached or interfering pole extensions removed in no time at all – so every workpiece has its own individual clamping device in no time at all.
For five-sided machining, the workpiece can be exposed with pole extensions.
Complex structures of workpieces that are difficult to clamp can be incorporated into the magnetically active surface via pole plates.
Our pole extensions are made of high-quality special steel and have the best magnetic flux properties – technically perfect and durable.
Palletizing magnetic chucks
Automation has also become indispensable in mechanical processing.
To keep machine downtimes as short as possible, palletizing and zero-point clamping systems are used on eroding, milling and grinding machines.
This allows the user to clamp the workpiece already outside the machine, so that a stock of clamped workpieces can be created for the machining machine.
External clamping takes place on pallets, which can be picked up in the machine with repeat accuracy.
These pallets are then fed into the machine either manually or automatically.
The magnetic chucks described are suitable for use with palletizing systems from all manufacturers.
For the production of self-supporting magnetic pallets, the reference elements can also be installed directly in the magnetic clamping plate.
We also supply ready-to-use magnetic pallets equipped with original clamping and positioning elements for all systems.
For heavy-duty machining and large workpieces, we recommend electro-permanent square-pole technology in combination with UniLock-R zero-point clamping systems.
Sinusoidal
Lamella plates
Magnetic clamping blocks
Permanent magnetic clamping blocks have 2 or 3 magnetic clamping surfaces which cannot be switched. They are used to clamp very fine parts or materials that are difficult to magnetize, such as high-alloy chrome steel or carbide. After machining, the block with the clamped workpiece can be completely removed from the machine for testing purposes.
Clamping blocks are available in standard versions and in reinforced versions for heavy workpieces. Magnetic blocks are mainly used for grinding, measuring and wire cutting.
Magnetic clamping balls in top quality are used to hold parts in the optimum working position during laser welding, polishing and assembly. Depending on the workpiece geometry and weight, swivel angles of up to 90° can be set.
Pole reversal control unit
Electric magnetic chucks are operated on pole reversal control units.
These devices make it possible to regulate the holding force and demagnetize workpieces.
Pole reversal controllers can be supplied as panel-mounted or table-top units.
Attention should be paid to the voltage and power of the solenoid.
SPSG-TG pole reversal control units in a desktop housing are ideal for retrofitting electro-magnetic chucks . Installation requires minimal effort. The device is simply plugged into a 230V mains supply. Mains cable with safety plug and hand lever are included in the scope of delivery.
Load lifting magnets
Permanent lifting magnet SPLM
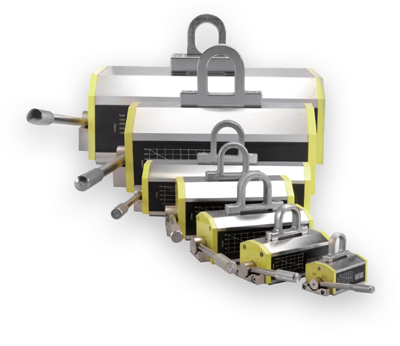
Permanent load lifting magnets for lifting ferromagnetic material, bar material, cold-rolled.
The lifting magnets are available from a size of LxWxH 130 x 70 x 60 mm up to LxWxH 496 x 160 x 140 mm.
- Safety factor of at least 3
- Suitable for flat and round material
- Maintenance-free construction
- The safety interlock prevents unintentional switching off
- On and off switch with one-hand operation
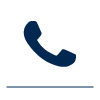
What can we do for you?
By using our products and services, our customers increase the productivity of their production by up to 100 % and at the same time significantly reduce their production costs.