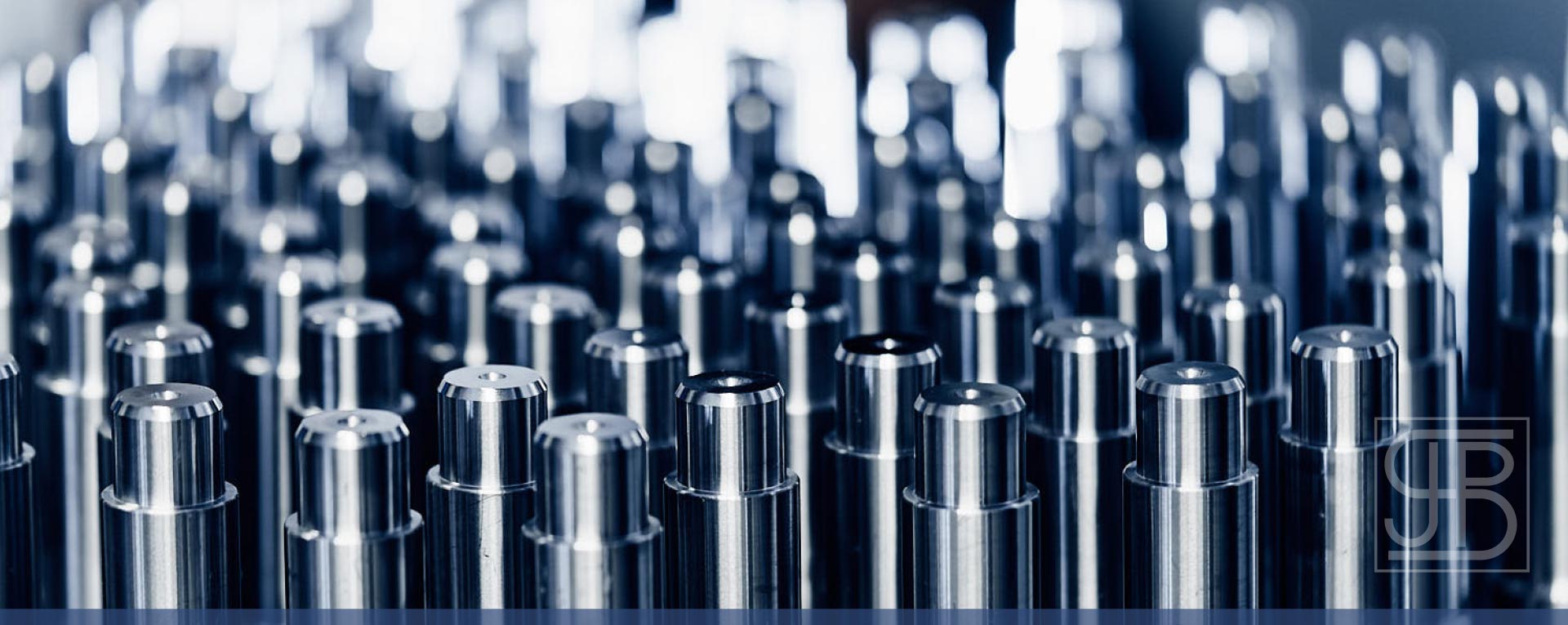
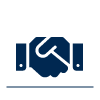
Plasma nitriding | Plasma nitriding technology
Distortion-free surface hardening for highly stressed components
We guarantee plasma nitriding competence since 1988. We apply our quality standards from the clamping technology to our hardening process.
Certified according to DIN EN ISO 9001:2015
What can we do for you?
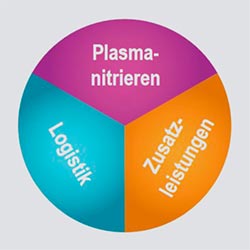
Spreitzer offers the trend-setting plasma nitriding technology in the ionic process as a service for you. This surface hardening process in a vacuum using ionized and reactive gases, is particularly characterized by low distortion, wear resistance and dimensional stability. It is mainly used for warpage-sensitive and highly stressed components.
Individual support
Customer-oriented thinking and acting is always in the foreground at Spreitzer. Each customer is served individually. We see ourselves as a service provider and the satisfaction of our customers is our top priority. We are specialist in this field and are glad to share our expertise with you on any plasma nitriding issue.
- Strengths:
- Our core competence lies in the fast and uncomplicated processing of small quantities, spare parts and sample parts.
- Your high-quality components are in good hands with us.
Plasma nitriding using the ionic process
The main advantages of plasma nitriding by the ionic process include the improvement of friction and sliding properties, the creation of corrosion-resistant coatings and the great lack of distortion. Mainly, finish-machined components are plasma-nitrided, and after this thermochemical heat treatment they are not subjected to any or only minor mechanical manufacturing operations such as grinding. This is an important economic and technical consideration for the metalworking industry.
All common steel, cast iron and sintered materials can be plasma nitrided. Both unalloyed and low- and high-alloy steels are suitable. We treat all workpieces, even long or geometrically complicated shapes and parts.
The advantages of the IONIC process
- low treatment temperature at 350°C to 600°C
- Dimensional stability and low warpage
- High hardness penetration
- High compressive strength, increased torsional strength
- Increased service life even under extreme load
- increased fatigue strength
- lower roughness and clean surfaces
- Improvement of sliding, friction and emergency running properties
- no pitting, low-noise operation (for gear parts)
- increased wear resistance
- increased corrosion resistance
- Treatment of certain workpiece surfaces (partial hardening) possible
- Environmental friendliness
The main industry sectors:
- Tool and mold making
- Mechanical engineering & plant construction
- Jig and fixture construction
- Automotive supply industry
- Automation and plant engineering
The main areas of application:
- Piston
- Spindles and gears
- Gear parts
- Guides and guide rails
- Hydraulic components
- Tools and dies
Process and procedure
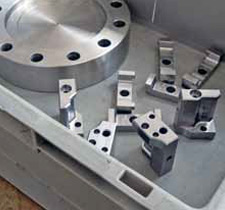
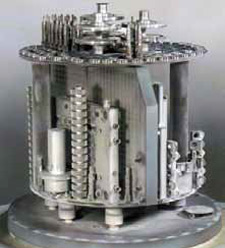
1. Information required for your order:
- Steel designation / material number
- Indication of possible pre-treatment of the parts
- Desired nitriding hardness depth (NHT) in mm
- Desired surface hardness in HV1
- Thickness of the compound layer in μm (optional)
- Possible footprint; in case of partial treatment, the required hardness ranges shall be marked. Areas that are not to be cured can be covered.
2. Part preparation for optimum treatment
- The parts must be delivered metallically bright, without paint, rust and scale.
3. Runtime
- For our customers we have two plants in our house as well as further plants outside our house.
Titanium Nitride Implanting
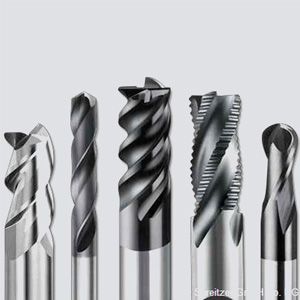
Titanium nitride implantation of cutting tools
This process is used for surface hardening of HSS tools. The treatment is carried out in a special form during the normal hardening process within our plasma nitriding facilities.
- Increased surface hardness
- Increased surface density, low coefficient of friction
- No geometric and dimensional changes to the mold
- Higher feed per minute (up to 100%)
- Regrinding possible
- Cost savings of up to 75% compared to coating processes
Attachment 1
- Inner dimension/filling dimension: Ø 450 x 600 mm
- Filling: 4 x weekly
- Standard runtime: 36 hours
Enclosure 2
- Inner dimension/filling dimension: Ø 650 x 1000 mm
- Filling: 3 x weekly
- Standard runtime: 60 hours

Plant external
- Inner dimension/filling dimension: Ø 1200 x 2500 mm
- Filling: 3 x weekly
- Standard runtime: 60 hours
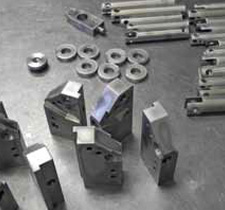
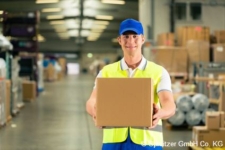
4. Additional services
- Covering work for partial treatment
- Hardness log for your complete documentation
- Sandblasting of your workpieces after the hardening process
- HM coating of clamping surfaces on clamping jaws and collets
5. Prizes
Prices for our plasma nitriding services are available upon request by e-mail or fax. We will be happy to provide you with a non-binding offer.
6. Logistics (pick-up and delivery service)
On request, we organize the collection and delivery of your goods by our reliable logistics partners.
We provide regular customers with one of our transport boxes. For details please visit
www.spreitzer.de/logistik
or give us a call.
By the way:
New customers receive their first order free of charge as a trial treatment up to a delivery weight of 10 kg. Test our performance. Contact us.
Wage treatment
Request surface treatment
Nitriding – Nitriding hardening – Carbonitriding Please contact us. For the latest information on the process and the material table, please refer to our PDF brochure.
Note: All fields marked with an * must be completed
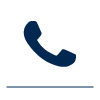
What can we do for you?
Reduce your production costs. Measuring tasks solved precisely within seconds.