
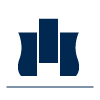
VACUUM CLAMPING TECHNOLOGY
We offer suitable solutions in the field of vacuum clamping technology, vacuum plates, vacuum chucks. Process-reliable clamping of flat metal workpieces, minimum set-up times and distortion-free work, e.g. in CNC machining centres.
MODULAR VACUUM CLAMPING SYSTEM, VACUUM CHUCKS
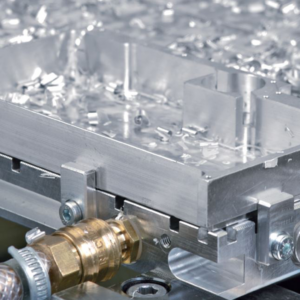
The vacuum plate is particularly suitable for process-reliable clamping of flat metal workpieces with flat undersides on CNC machining centres and guarantees minimum set-up times. Even components that are difficult to clamp mechanically can be fixed uncomplicatedly, quickly, distortion-free and precisely with the help of the vacuum clamping system.
The vacuum clamping technology, vacuum clamps enable:
- Short set-up times
- High holding force
- High precision
FLEXIBLE SETUP OF A COMPLETE VACUUM CLAMPING SYSTEM
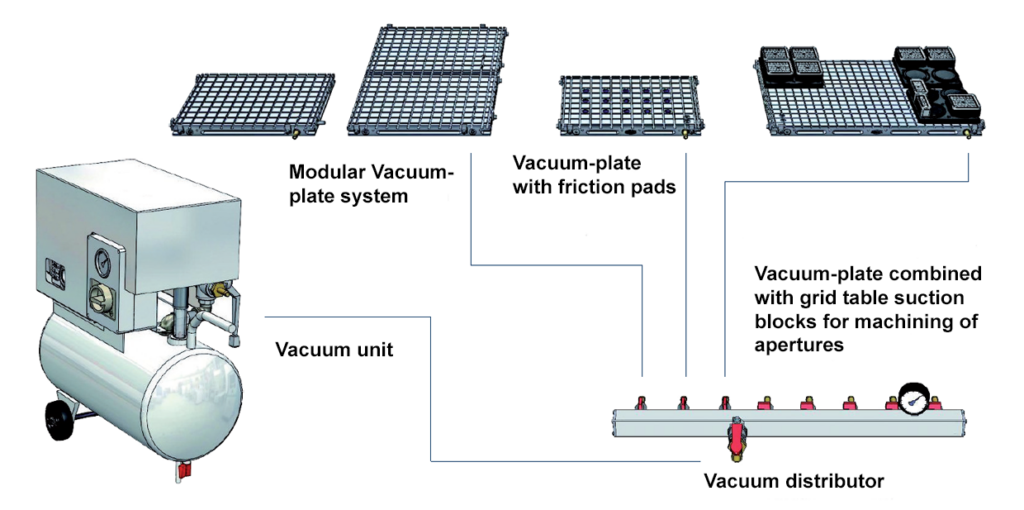
VACUUM PLATES AND VACUUM CHUCKS
The vacuum plate can be quickly attached to the machine table by means of clamping claws or a zero-point system.
The modular design ensures maximum flexibility through easy handling and any combination of the various product versions.
The complexity of the workpiece geometry, the type and method of machining and the horizontal forces to be absorbed determine the selection of the vacuum clamping plate version.
Exclusive SPREITZER features:
Optional friction pads result in a significantly higher absorption of transverse forces
- High horizontal holding forces (up to 30% increase compared to vacuum plates without friction pads)
- No additional force of the friction pads on the workpiece
- Oil and ozone resistant, individually replaceable in case of wear
- Activation and deactivation automatically via vacuum supply
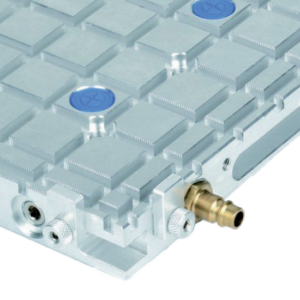
Vacuum plate with friction pads
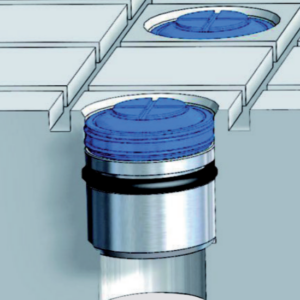
Active friction pad – vacuum plate

Inactive friction pads – vacuum plate
VACUUM UNIT AND VACUUM GENERATOR

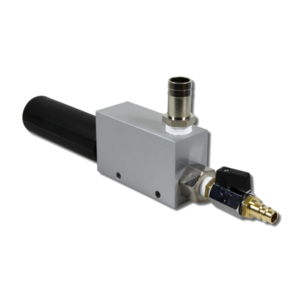
The vacuum generator works with compressed air. No additional connections are required on the machine.
SECURE CLAMPING OF COMPLEX WORKPIECES
When machining simple workpieces, a coarse grid dimension is sufficient. Complex workpieces with openings must be additionally sealed with a sealing cord at the corresponding points to ensure the system vacuum. When using a fine grid dimension, this sealing cord can be positioned close to the openings and recesses. This seals them flexibly and minimises clamping force losses.
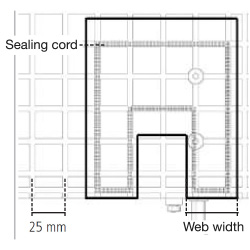
Simple workpiece
- Geometrically simple structure
- Few webs and recesses/openings
- Bar width > 30 mm
Recommendation: grid size 25 x 25 mm
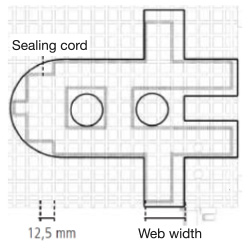
Complex workpiece
- Geometrically complex structure
- Many webs and recesses/breakthroughs
- Bar width < 30 mm
Recommendation: grid size 12.5 x 12.5 mm
CLAMPING DEVICE
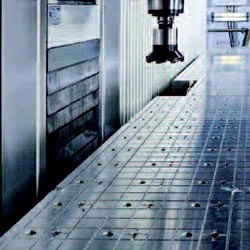
Clamping device for aerospace
The sometimes very complex workpiece geometries in the aerospace industry usually require a special clamping solution adapted to the application. Maximum precision and gentle machining of the workpiece are particularly in demand.
Within the scope of special project planning, we have already developed successful solutions for customer-specific projects on several occasions. With the vacuum plate, even very thin workpieces can be fixed without damage and with process reliability. Set-up time minimisation and the high degree of flexibility are additional arguments in favour of the vacuum clamping system.
MILLING THROUGH
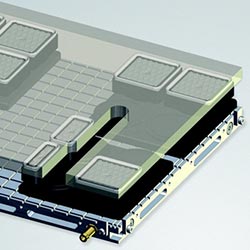
Milling through a workpiece with vacuum plate and grid table suction cups
The use of grid table suction cups makes it possible to produce apertures when machining workpieces. In the first step, machining is carried out with small height tolerances on the workpiece clamped on the vacuum plate.
In the second step, the grid table suction cups are inserted directly into the grid of the vacuum plate and the suction cups are arranged according to the position of the drill holes. In this way, the workpiece can be drilled through without damaging the vacuum plate or the component itself.
CLAMPING
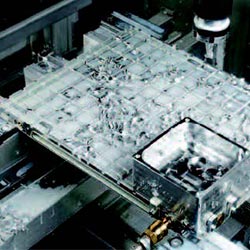
Efficient clamping of aluminium cubes
The application shows a vacuum plate in use on a CNC machining centre for metal processing. It is fixed on the machine table with the help of mechanical clamping devices. By using vacuum, the thin-walled underside of the workpiece can be clamped precisely and without distortion. This enables efficient 5-axis machining in one clamping.
The powerful AGG vacuum unit is used to generate the vacuum. Due to its compact design, it is mobile and can be moved ergonomically to the place of use by means of a handle and rollers.
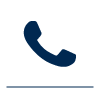
WHAT CAN WE DO FOR YOU?
By using our products and services, our customers increase the productivity of their production by up to 100% and at the same time reduce their production costs to a large extent.